CASE STUDY
Enhancing Training Potential for Field Service Engineers using VR Technology
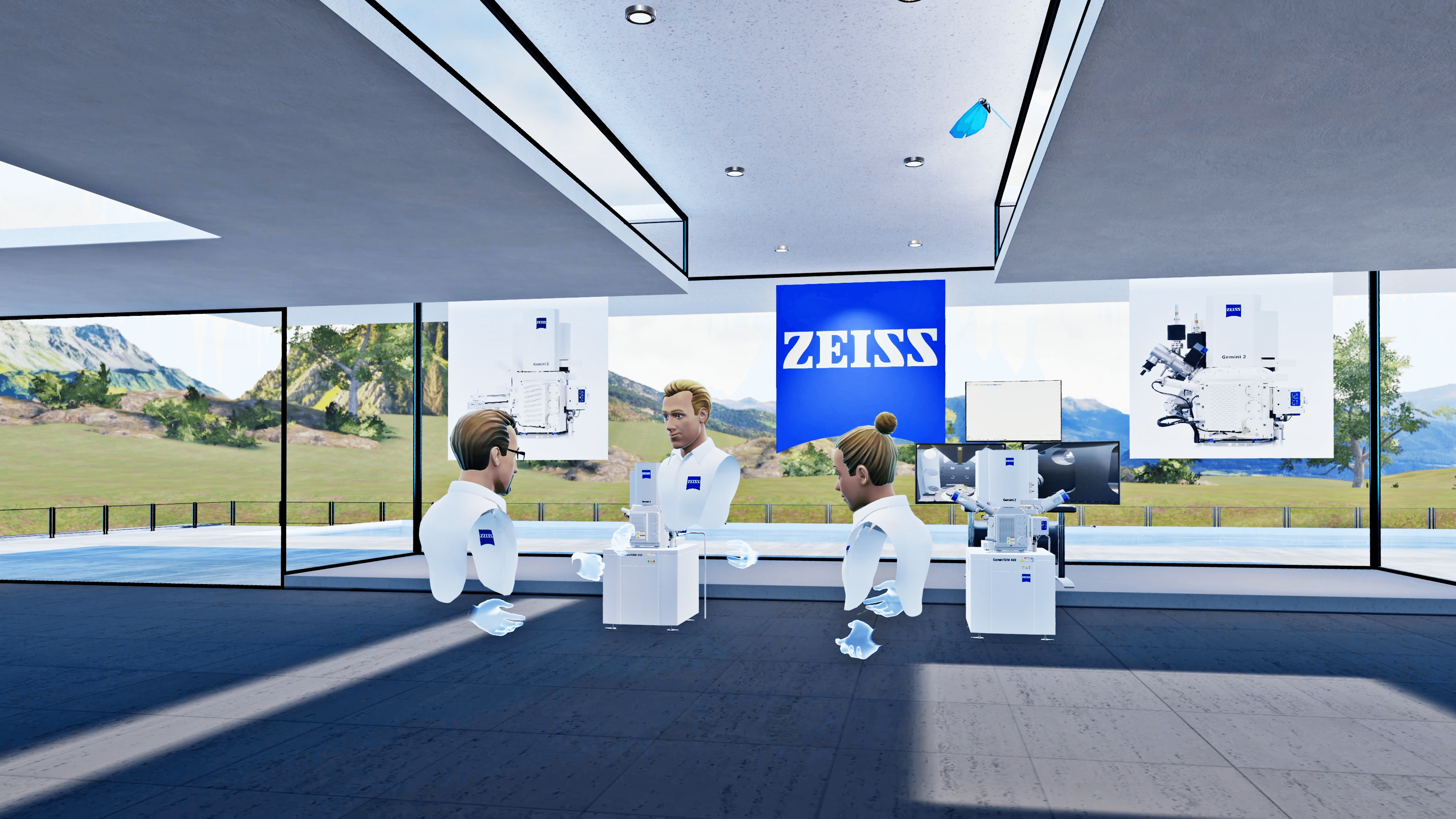
Embracing a Virtual Solution
As the world’s leading manufacturer of microscope systems for life sciences, materials and industrial research, as well as education and clinical practice, ZEISS Research Microscopy Solutions identified virtual reality (VR) as a global strategic key component of its training for its Field Service Engineers (FSEs). ZEISS partnered with realworld one to help them achieve this initiative.
Providing excellent support to customers requires consistent training for FSEs. In-person training carried a significant financial and opportunity cost due to travel expenses and time spent away from customers. This also presented a risk of equipment damage, with FSE’s only having minimal opportunity to interact with microscopes. ZEISS sought alternative approaches that could improve training outcomes, minimize expenses, and align with their mission to advance standards of care. Virtual Reality offered a centralized solution to achieve these objectives.
“We quickly determined VR would play a key role in helping us reach the goals we set for the service department over the next years. A more efficient way of training our FSEs through immersive technology improves our service quality greatly.”
Lothar Bihlmaier, Head of Global Support, ZEISS Research Microscopy Solutions
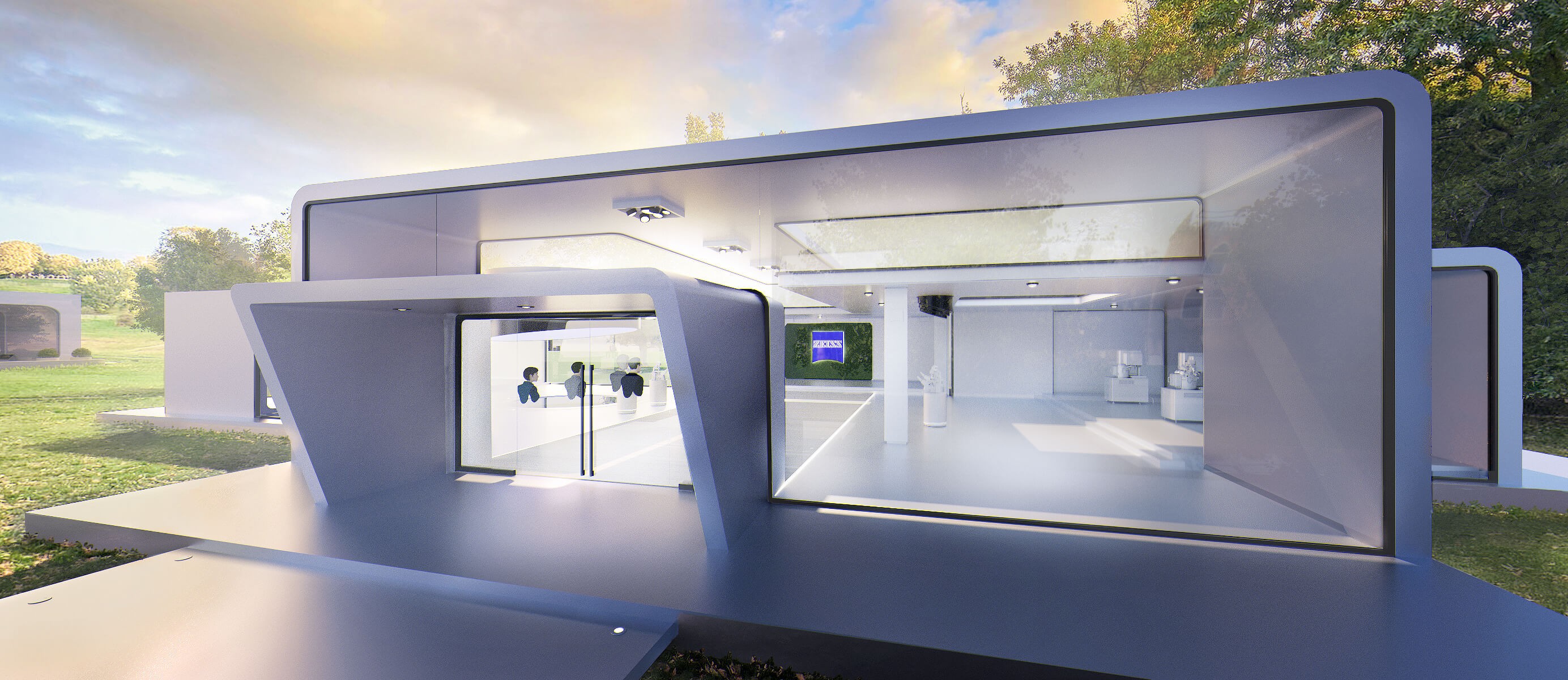
The realworld one software platform offers users a suite of features that foster collaboration and flexibility across their virtual workspaces. By leveraging the multi-user function, teams can interact, communicate, and invite other users to join meetings in real time, regardless of their location. The CAN functionality enables users to preserve valuable data by recording and sharing their interactive virtual content, such as training sessions and product demonstrations.
Users who don’t have a VR headset aren’t restricted from the platform either. Using non-VR mode, individuals can access realworld one’s virtual environments and connect with other VR users through a complementary desktop application.
The platform also permits users to upload and share various filetypes, such as CAD files, PDFs, presentations, and images, in VR. Additionally, the platform provides support for numerous languages, thus enabling further global interconnectivity.
Virtual Technology, Real Benefits
VR has enhanced ZEISS’s training flexibility by providing a consistent learning format applicable to both experienced and inexperienced trainees. In addition to streamlining the learning experience, immersive training offers a variety of other benefits:
Efficiency: VR training strengthens muscle memory and increases knowledge retention up to 90% compared to 20% with video instruction.
Faster onboarding: By interacting with ZEISS’ products and practicing procedures in VR, new FSEs quickly gain the hands-on knowledge and experience necessary to become a certified FSE.
Repeatability: FSEs can easily memorize actions through repeated practice sessions at no extra cost to ZEISS.
Better feedback: Using realworld one’s CAN functionality, all VR sessions can be recorded and reviewed to provide trainees with feedback.
Smaller carbon footprint: ZEISS aims to be carbon neutral by 2022. Removing the need to fly in FSEs has reduced ZEISS’ carbon footprint.
Shaping the Future with VR
VR’s scalability makes it easy for ZEISS to implement the technology in a variety of applications, and ZEISS is currently extending VR across the company to other departments. Its sales, marketing, and support teams will be able to use VR for content, product presentations, and training purposes. ZEISS is also working with realworld one to develop a VR showroom for clients to showcase its products. Expanding VR through these strategies will continually reduce costs and improve operational efficiencies for ZEISS.
Additionally, ZEISS is creating an information portal in VR with decision trees, fault trees, a spare catalogue, and more. Employees will be able to use the portal for on-the-job task assistance. Immersive technology continues to offer Zeiss numerous possibilities to streamline its operations and is quickly becoming a valuable tool for its employees and customers alike.
About ZEISS
ZEISS is an internationally leading technology enterprise operating in the fields of optics and optoelectronics. For its customers, ZEISS develops, produces and distributes highly innovative solutions for industrial metrology and quality assurance, microscopy solutions for the life sciences and materials research, and medical technology solutions for diagnostics and treatment in ophthalmology and microsurgery. Founded in 1846 in Jena, the company is headquartered in Oberkochen, Germany, employing over 34,000 people worldwide.
As the world’s leading manufacturer of microscope systems for life sciences, materials and industrial research, as well as education and clinical practice, ZEISS Research Microscopy Solutions identified virtual reality (VR) as a global strategic key component of its training for its Field Service Engineers (FSEs). ZEISS partnered with realworld one to help them achieve this initiative.
Providing excellent support to customers requires consistent training for FSEs. In-person training carried a significant financial and opportunity cost due to travel expenses and time spent away from customers. This also presented a risk of equipment damage, with FSE’s only having minimal opportunity to interact with microscopes. ZEISS sought alternative approaches that could improve training outcomes, minimize expenses, and align with their mission to advance standards of care. Virtual Reality offered a centralized solution to achieve these objectives.
“We quickly determined VR would play a key role in helping us reach the goals we set for the service department over the next years. A more efficient way of training our FSEs through immersive technology improves our service quality greatly.”
Lothar Bihlmaier, Head of Global Support, ZEISS Research Microscopy Solutions
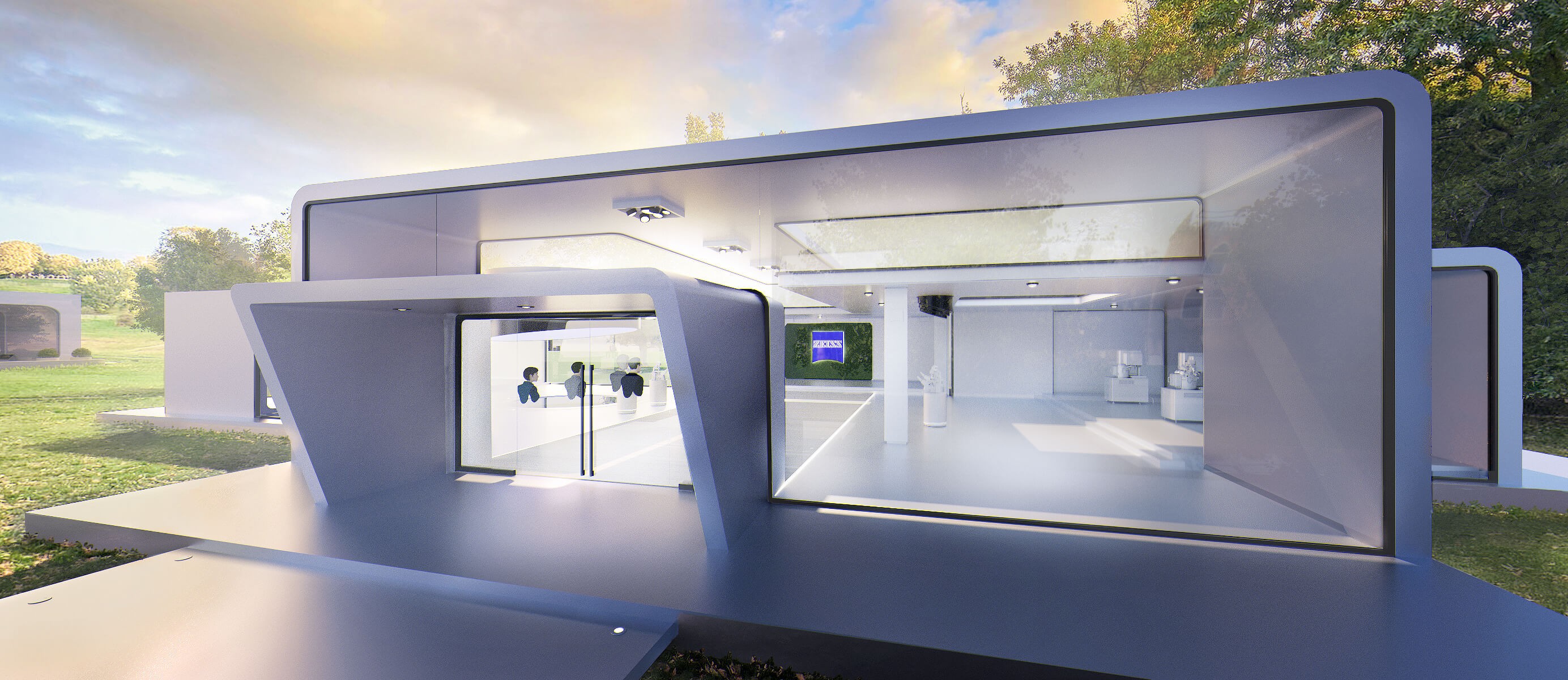
The realworld one software platform offers users a suite of features that foster collaboration and flexibility across their virtual workspaces. By leveraging the multi-user function, teams can interact, communicate, and invite other users to join meetings in real time, regardless of their location. The CAN functionality enables users to preserve valuable data by recording and sharing their interactive virtual content, such as training sessions and product demonstrations.
Users who don’t have a VR headset aren’t restricted from the platform either. Using non-VR mode, individuals can access realworld one’s virtual environments and connect with other VR users through a complementary desktop application.
The platform also permits users to upload and share various filetypes, such as CAD files, PDFs, presentations, and images, in VR. Additionally, the platform provides support for numerous languages, thus enabling further global interconnectivity.
Virtual Technology, Real Benefits
VR has enhanced ZEISS’s training flexibility by providing a consistent learning format applicable to both experienced and inexperienced trainees. In addition to streamlining the learning experience, immersive training offers a variety of other benefits:
Efficiency: VR training strengthens muscle memory and increases knowledge retention up to 90% compared to 20% with video instruction.
Faster onboarding: By interacting with ZEISS’ products and practicing procedures in VR, new FSEs quickly gain the hands-on knowledge and experience necessary to become a certified FSE.
Repeatability: FSEs can easily memorize actions through repeated practice sessions at no extra cost to ZEISS.
Better feedback: Using realworld one’s CAN functionality, all VR sessions can be recorded and reviewed to provide trainees with feedback.
Smaller carbon footprint: ZEISS aims to be carbon neutral by 2022. Removing the need to fly in FSEs has reduced ZEISS’ carbon footprint.
Shaping the Future with VR
VR’s scalability makes it easy for ZEISS to implement the technology in a variety of applications, and ZEISS is currently extending VR across the company to other departments. Its sales, marketing, and support teams will be able to use VR for content, product presentations, and training purposes. ZEISS is also working with realworld one to develop a VR showroom for clients to showcase its products. Expanding VR through these strategies will continually reduce costs and improve operational efficiencies for ZEISS.
Additionally, ZEISS is creating an information portal in VR with decision trees, fault trees, a spare catalogue, and more. Employees will be able to use the portal for on-the-job task assistance. Immersive technology continues to offer Zeiss numerous possibilities to streamline its operations and is quickly becoming a valuable tool for its employees and customers alike.
About ZEISS
ZEISS is an internationally leading technology enterprise operating in the fields of optics and optoelectronics. For its customers, ZEISS develops, produces and distributes highly innovative solutions for industrial metrology and quality assurance, microscopy solutions for the life sciences and materials research, and medical technology solutions for diagnostics and treatment in ophthalmology and microsurgery. Founded in 1846 in Jena, the company is headquartered in Oberkochen, Germany, employing over 34,000 people worldwide.
As the world’s leading manufacturer of microscope systems for life sciences, materials and industrial research, as well as education and clinical practice, ZEISS Research Microscopy Solutions identified virtual reality (VR) as a global strategic key component of its training for its Field Service Engineers (FSEs). ZEISS partnered with realworld one to help them achieve this initiative.
Providing excellent support to customers requires consistent training for FSEs. In-person training carried a significant financial and opportunity cost due to travel expenses and time spent away from customers. This also presented a risk of equipment damage, with FSE’s only having minimal opportunity to interact with microscopes. ZEISS sought alternative approaches that could improve training outcomes, minimize expenses, and align with their mission to advance standards of care. Virtual Reality offered a centralized solution to achieve these objectives.
“We quickly determined VR would play a key role in helping us reach the goals we set for the service department over the next years. A more efficient way of training our FSEs through immersive technology improves our service quality greatly.”
Lothar Bihlmaier, Head of Global Support, ZEISS Research Microscopy Solutions
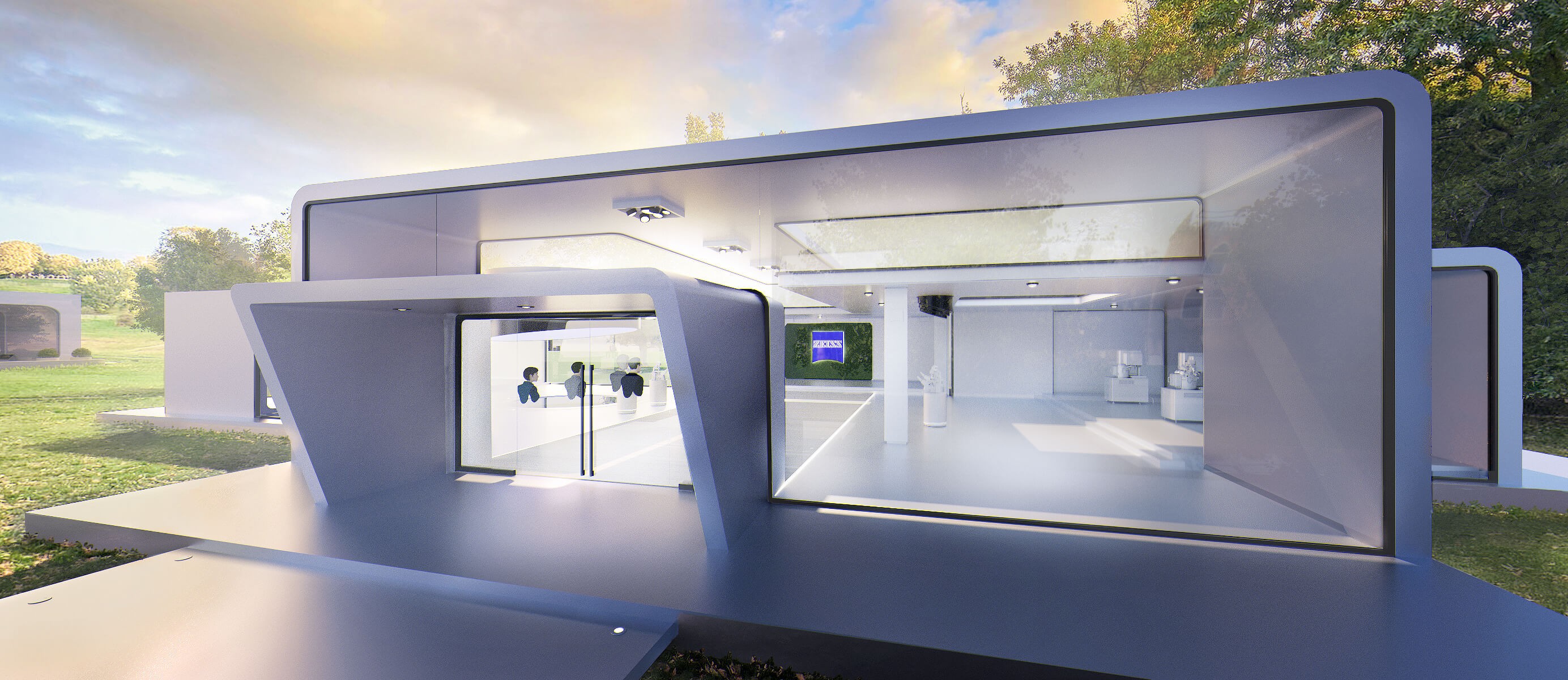
The realworld one software platform offers users a suite of features that foster collaboration and flexibility across their virtual workspaces. By leveraging the multi-user function, teams can interact, communicate, and invite other users to join meetings in real time, regardless of their location. The CAN functionality enables users to preserve valuable data by recording and sharing their interactive virtual content, such as training sessions and product demonstrations.
Users who don’t have a VR headset aren’t restricted from the platform either. Using non-VR mode, individuals can access realworld one’s virtual environments and connect with other VR users through a complementary desktop application.
The platform also permits users to upload and share various filetypes, such as CAD files, PDFs, presentations, and images, in VR. Additionally, the platform provides support for numerous languages, thus enabling further global interconnectivity.
Virtual Technology, Real Benefits
VR has enhanced ZEISS’s training flexibility by providing a consistent learning format applicable to both experienced and inexperienced trainees. In addition to streamlining the learning experience, immersive training offers a variety of other benefits:
Efficiency: VR training strengthens muscle memory and increases knowledge retention up to 90% compared to 20% with video instruction.
Faster onboarding: By interacting with ZEISS’ products and practicing procedures in VR, new FSEs quickly gain the hands-on knowledge and experience necessary to become a certified FSE.
Repeatability: FSEs can easily memorize actions through repeated practice sessions at no extra cost to ZEISS.
Better feedback: Using realworld one’s CAN functionality, all VR sessions can be recorded and reviewed to provide trainees with feedback.
Smaller carbon footprint: ZEISS aims to be carbon neutral by 2022. Removing the need to fly in FSEs has reduced ZEISS’ carbon footprint.
Shaping the Future with VR
VR’s scalability makes it easy for ZEISS to implement the technology in a variety of applications, and ZEISS is currently extending VR across the company to other departments. Its sales, marketing, and support teams will be able to use VR for content, product presentations, and training purposes. ZEISS is also working with realworld one to develop a VR showroom for clients to showcase its products. Expanding VR through these strategies will continually reduce costs and improve operational efficiencies for ZEISS.
Additionally, ZEISS is creating an information portal in VR with decision trees, fault trees, a spare catalogue, and more. Employees will be able to use the portal for on-the-job task assistance. Immersive technology continues to offer Zeiss numerous possibilities to streamline its operations and is quickly becoming a valuable tool for its employees and customers alike.
About ZEISS
ZEISS is an internationally leading technology enterprise operating in the fields of optics and optoelectronics. For its customers, ZEISS develops, produces and distributes highly innovative solutions for industrial metrology and quality assurance, microscopy solutions for the life sciences and materials research, and medical technology solutions for diagnostics and treatment in ophthalmology and microsurgery. Founded in 1846 in Jena, the company is headquartered in Oberkochen, Germany, employing over 34,000 people worldwide.